Introduction:
In diverse sectors like paint, coatings, ink, pigment, and pesticide industries, achieving the perfect particle size is critical for product quality. Bead mills are at the heart of this process, but their efficiency varies based on multiple factors. This blog delves into how particle analysis, coupled with an understanding of bead mill mechanics, can fine-tune this process for optimal results.
Understanding Bead Mill Structure and Function:
A bead mill consists of a milling chamber filled with grinding beads and a mechanism to agitate these beads. The material to be milled is pumped through this chamber, where the motion of the beads breaks it down into fine particles. The design of the mill – including the size and material of the beads, the agitator speed, and the flow rate of the material – greatly influences the grinding efficiency.
How Beads Work Inside the Bead Mill:
The beads within the mill play a pivotal role. As the agitator rotates, it creates shear and impact forces that grind the particles to the desired size. The efficiency of this process depends on the size, density, and material of the beads. For example, smaller beads are better for achieving finer particles, but require a higher energy input.
Impact of Beads on Grinding and Particle Size:
The choice of beads is crucial. Harder beads, like those made of zirconium oxide, are effective for grinding tough materials but may cause more wear on the mill. Softer beads, like those made of glass, might be less efficient but are gentler on the milling apparatus. Balancing these factors is key to optimizing milling performance.
Discrete particle size distribution
Optimizing the grinding process involves striking the right balance between milling efficiency and effectiveness. If the focus is solely on efficiency, the result is a high-quality end product characterized by precisely defined particle size boundaries and a distinct particle size distribution. In such scenarios, the mill operates at a slower pace, applying minimal energy to the material. This approach has the advantage of reducing wear on the mill’s components. However, it also has downsides: it diminishes the production capacity and escalates energy expenses due to the prolonged milling time needed to achieve the specific particle size distribution.
On the contrary, a grinding process prioritizing effectiveness results in a high output and reduced residence time of the product in the mill. However, this is achieved at the cost of increased wear and tear due to the high operating speeds. This frequent need for repair and replacement of worn or damaged parts, including the grinding media in wet milling applications, can lead to escalated costs and downtime, potentially negating the benefits of the increased output. Additionally, the wear on mill components poses a risk of contaminating the material, which can adversely affect the quality of the final product.
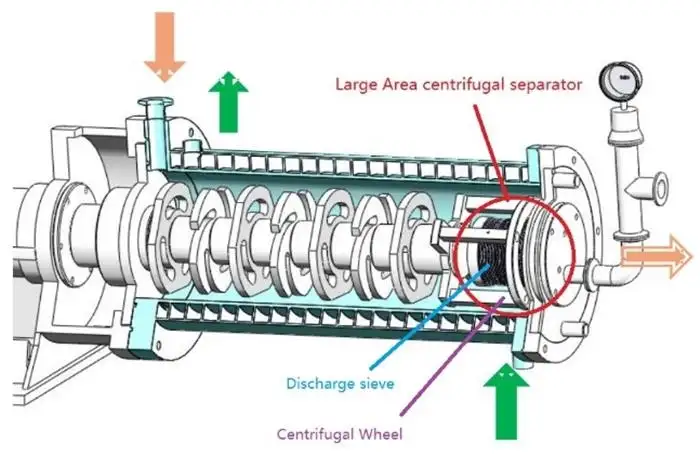
The operating parameters of a mill play a pivotal role in determining the balance between efficiency and effectiveness in the milling process. By gaining a comprehensive understanding of your specific process requirements and the characteristics of the material being processed, it’s possible to develop a milling approach that harmoniously balances these two aspects. This not only leads to time and cost savings but also guarantees consistent and repeatable outcomes.
Understanding Material Properties for Optimal Milling
To achieve a well-balanced milling process, it’s essential to thoroughly understand the material you are working with. The first step in optimizing your milling process involves identifying the initial properties of your feed material, as well as the desired properties of your final product. Factors such as the type of material, particle size distribution, Bulk density, fluidity, brittleness, abrasiveness, temperature sensitivity, hygroscopicity, moisture content, volatile matter content, and chemical corrosion all play a significant role in determining the appropriate equipment selection and operating parameters.
Conducting a particle characterization analysis is crucial to gain a deeper understanding of the feed material. This understanding can be pivotal in enhancing mill performance and maintaining consistent product quality. When developing or monitoring a milling process, the most critical physical properties to measure include:
Particle size
Particle shape
Surface properties
Mechanical properties, which encompass hardness, elasticity, modularity, adhesion, and friction
Charge properties
Particle microstructure, including whether the particles are solid or agglomerated
Understanding and measuring these properties allows for more informed decisions in the milling process, leading to optimized performance and product quality.
Utilizing Particle Size Analysis for Optimization:
Particle size analysis provides essential feedback on the milling process. By regularly analyzing the particle size distribution of output materials, adjustments can be made to the mill’s parameters for improved efficiency. This could involve changing the bead size, material, agitator speed, or even the flow rate of the material through the mill.
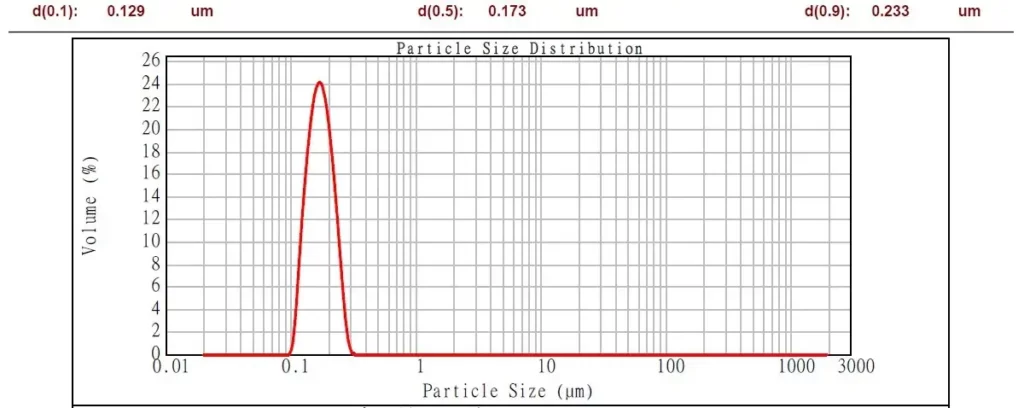
Here’s how to do it:
Sample Collection:
Collect samples directly from the bead mill output.
Ensure the samples are representative by collecting them at various stages or times during the milling process.
Handle samples carefully to avoid segregation or settling of particles, which can skew the results.
Sample Preparation:
Since the output is a liquid suspension, ensure the sample is well-mixed to maintain a uniform distribution of particles.
In some cases, dilution of the sample with an appropriate solvent might be necessary to suit the analysis technique.
Selection of Analytical Technique:
Laser Diffraction: Ideal for a wide range of particle sizes, this method measures particle size distribution based on light scattering patterns.
Dynamic Light Scattering (DLS): Best suited for nanoparticles, DLS analyzes the Brownian motion of particles to determine their size.
Ultrasonic Spectroscopy: Useful for highly concentrated suspensions, it measures particle size through ultrasonic attenuation and scattering.
Electron Microscopy: For detailed visualization and analysis of nano-sized particles, electron microscopy can be used, though it is more time-consuming and complex.
Conducting the Analysis:
Follow the specific protocols of the chosen analytical method.
Use calibrated instruments to ensure accuracy.
It’s often beneficial to conduct multiple analyses to ensure consistency and reliability of the results.
Data Interpretation:
Analyze the data to understand the particle size distribution, focusing on the median size, distribution width, and the presence of any aggregates or outliers.
Compare the results with the target specifications for the product.
Quality Control:
Assess if the particle size distribution meets the desired criteria for the end-use of the product.
Evaluate the consistency of the particle size across different samples.
Process Adjustment and Optimization:
If the particle size is not within the desired specifications, consider adjusting the bead mill parameters such as bead size, milling time, or agitation speed.
Document any changes made for continuous improvement and traceability.
Reporting:
Document the findings and methodology used.
Include this information in quality control records and use it for future reference and process optimization.
Particle analysis in the context of bead milling for liquid chemical grinding is critical for ensuring product quality and consistency. Regular monitoring and analysis help in maintaining the desired particle size distribution, which is crucial for the performance and functionality of the end product.
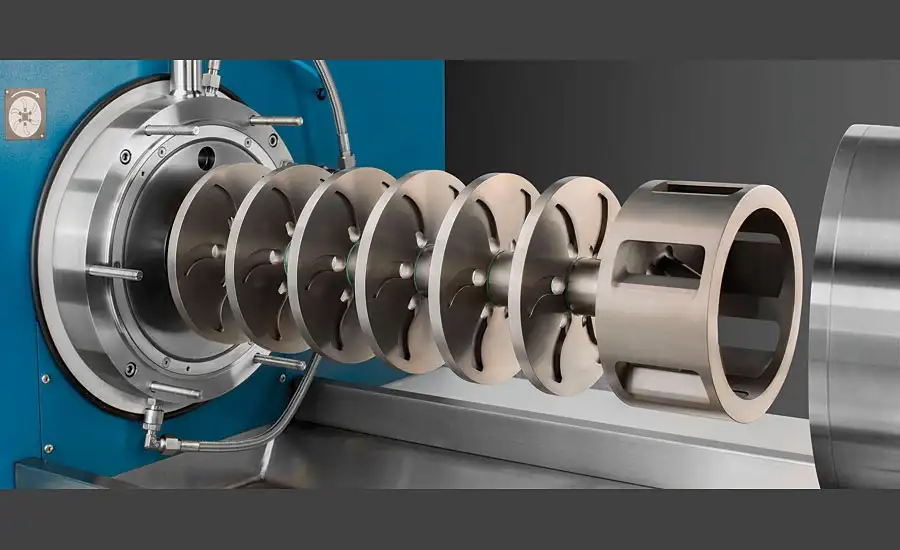
Case Studies in Various Industries:
Here, include specific examples from industries like paint, where achieving a smooth texture is crucial, or the ink industry, where the clarity and brightness of colors depend heavily on particle size. These case studies can illustrate how adjustments in bead choice and milling parameters led to significant improvements.
Conclusion:
Optimizing bead mill performance is a fine balance between the right bead selection, mill parameters, and understanding the material’s requirements. Particle analysis is a critical tool in this process, enabling manufacturers to achieve consistent, high-quality output tailored to the specific needs of their industry.