Paint sand mills, specifically horizontal bead mills, are game-changers in the coating and paint industry as continuous grinding machines, efficiency grinding equipment, and wet grinding machines for large flow ultrafine grinding. They mix and grind materials efficiently using a continuous grinding machine, ensuring a smooth finish with a high efficiency bead mill. These machines use tiny beads in a vertical sand mill to break down sand milled material, resulting in high-quality laboratory sand products.
Their design, featuring a vertical sand mill, allows for better control of particle size and distribution in products. This leads to improved performance in paints and coatings. Businesses benefit from faster production times and consistent results. Understanding how these mills work can help you choose the right products and equipment for your needs. Explore the benefits and features of products that make horizontal bead mills essential for any paint manufacturer.
Key Takeaways
- Understand how horizontal bead mills operate to optimize your production processes and improve efficiency in paint manufacturing products.
- Familiarize yourself with different types of horizontal bead mills products to choose the right model that meets your specific needs.
- Pay attention to key components of the mills and their products, as this knowledge will help in troubleshooting and maintenance tasks.
- Follow the operating guide closely to ensure safety and effective use of the products and equipment, preventing costly errors.
- Implement regular maintenance tips for your products to prolong the life of your bead mill and maintain consistent performance.
- Consider the applications of horizontal bead mills across various industries to identify new opportunities for your products and business.
How Horizontal Bead Mills Work
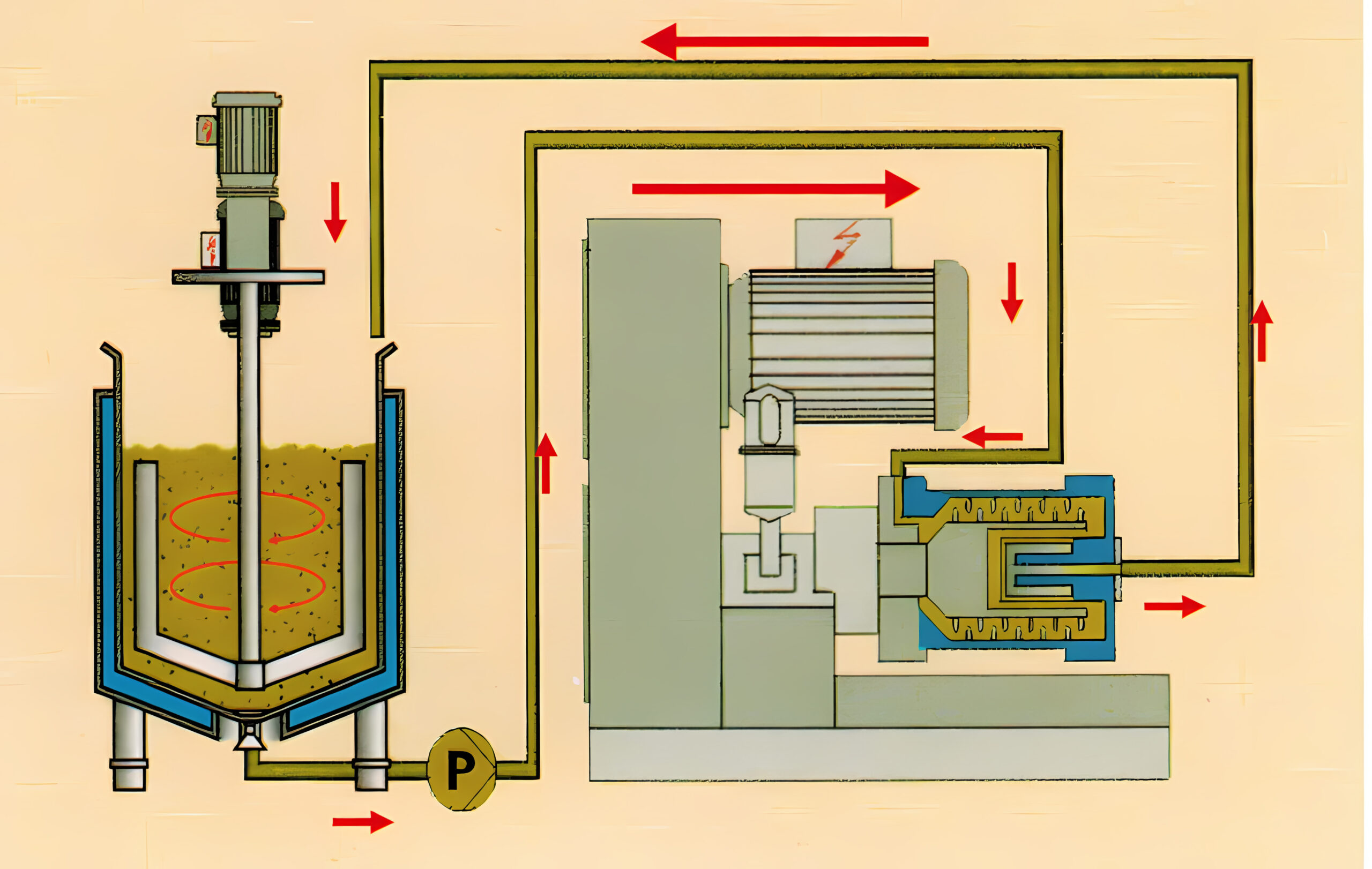
Feeding Process
Products enter the horizontal bead mill through a designated feeding system. The feed hopper holds the products before they move into the grinding chamber. Gravity or a pump typically moves these products into the barrel.
Once inside, the materials mix with the grinding medium. This medium usually consists of small beads made from ceramic or glass products. The size of these beads influences the grinding efficiency and final particle size of products.
The feeding process is crucial. Properly feeding materials ensures uniform mixing and effective grinding. Any inconsistency can lead to uneven results in the final products.
High-Speed Rotating Dispersers
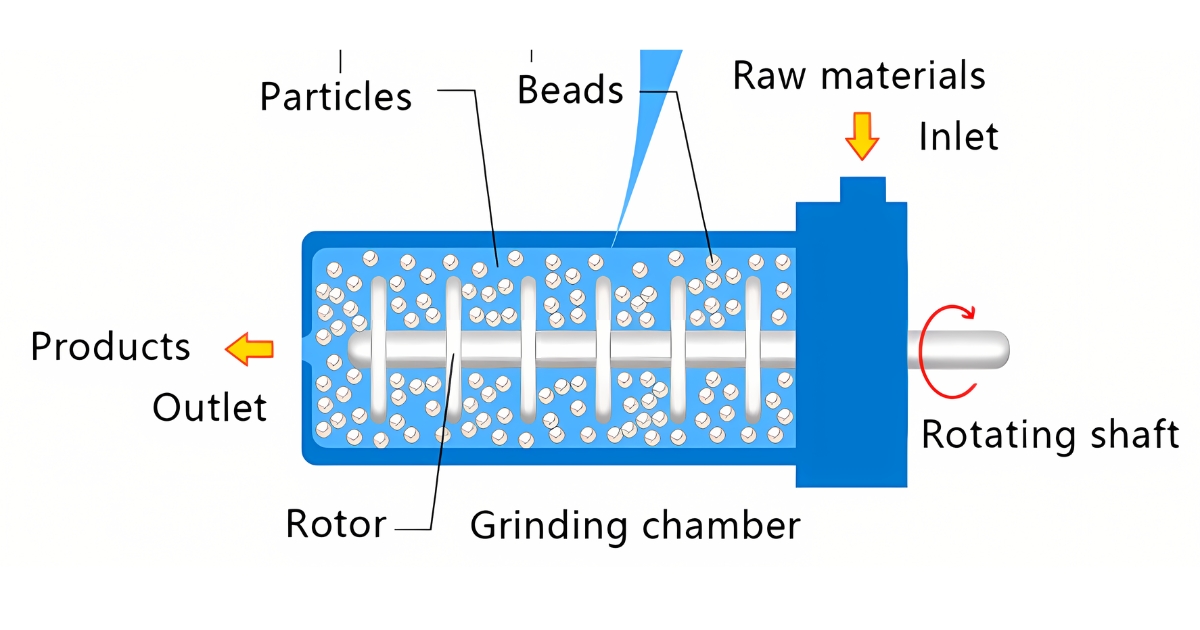
High-speed rotating dispersers play a key role in the grinding process for products. These components create intense shear forces that break down products and particles. The rotation speed of the products can reach thousands of revolutions per minute.
As the dispersers spin, they agitate the mixture of products, materials, and beads. This agitation leads to collisions between particles, which aids in size reduction of products. The faster the rotation, the more effective the grinding products become.
These dispersers are often adjustable. Operators can control their speed based on the desired outcome of products. Adjusting this speed allows for flexibility in achieving different particle sizes for products.
Dynamic Separators

Dynamic separators are essential for separating the grinding medium from the finished products. After grinding, a mixture of ground products and beads exists within the mill. The dynamic separator uses centrifugal force to separate these products efficiently.
As the mixture flows through the separator, heavier beads are pushed outward while lighter particles move toward the center, forming products. This separation occurs rapidly, minimizing downtime during production.
The design of dynamic separators varies by manufacturer. Some have multiple stages for enhanced separation efficiency. This design ensures that only finely ground products exit while retaining most of the grinding media inside.
Efficiency of Grinding Mechanism
The grinding mechanism in horizontal bead mills is highly efficient for products. It achieves fine particle sizes quickly for products compared to other milling methods. This efficiency stems from several factors, including bead size, dispersion speed, and products.
Fine particles result from repeated collisions between beads and materials, products of the interaction. The constant movement keeps particles suspended in the liquid phase, allowing for continuous grinding action of products.
Achieving superfine particle sizes for products often requires specific adjustments to parameters like bead size and mill speed. For example, smaller beads can produce finer particles for products but may require longer processing times.
This effectiveness makes horizontal bead mills ideal for various applications, including paint production, coatings, and products. Industries rely on these machines for consistent quality and performance of products.
Types and Variations
Ordinary Mill
Ordinary horizontal sand mills are among the most common types of products. They feature a simple design that includes a cylindrical chamber filled with grinding media products. The media products are typically made of ceramic or steel beads. This type works well for many applications.
The structure allows for effective dispersion of materials. The rotating shaft drives the media and products, which collides with the particles in the liquid. This collision breaks down the products and particles, achieving a uniform mixture.
Operationally, ordinary mills excel in low-viscosity materials. They are suitable products for paints and inks, where fine dispersion is crucial. However, their products may struggle with thicker materials due to their basic design.
Wheel-Pin Mill

Wheel-pin mills have a more complex structure than ordinary mills for products. They incorporate products, pins attached to a wheel that rotates within the chamber. This design increases the shear force applied to the products material.
The wheel-pin configuration improves particle size reduction of products compared to ordinary mills. It allows for better control over the dispersion process. This type is particularly effective for medium-viscosity products.
Applications include coatings and adhesives products, where precise particle size is essential. The adaptability of this mill to different viscosities makes it versatile in various industries and products.
Disc Mill
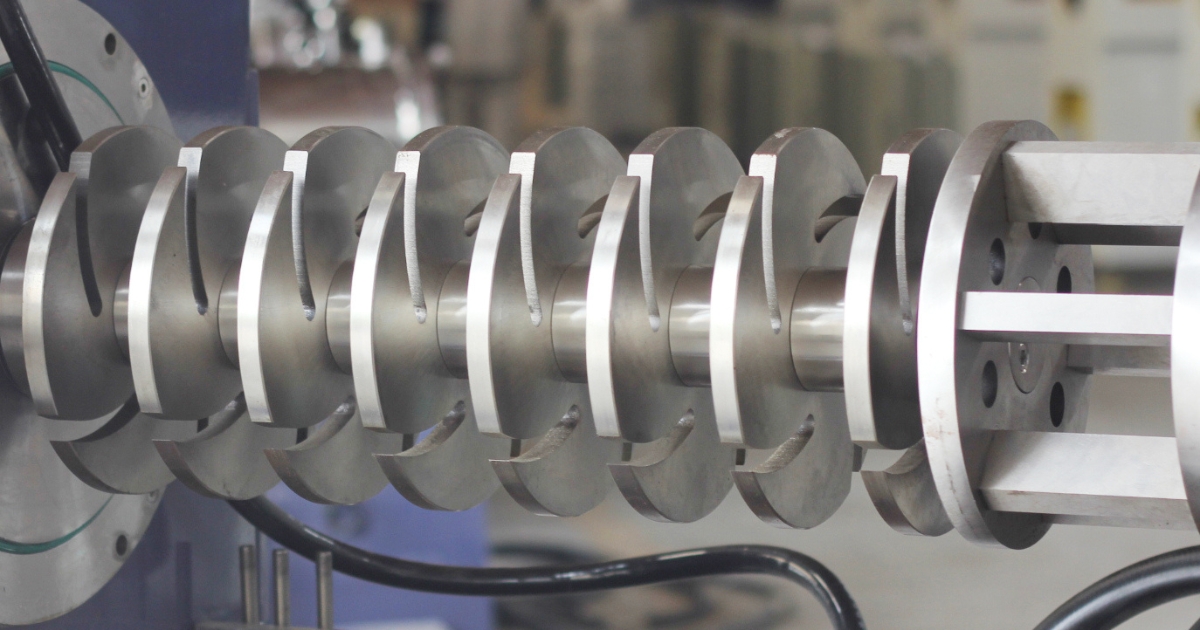
A disc horizontal bead mill typically consists of a cylindrical grinding chamber with a central shaft. Attached to the shaft are two or more discs that rotate in opposite directions. These discs are covered with grinding media (beads), which are small, hard spheres that help break down the material being processed.
Turbo Mill
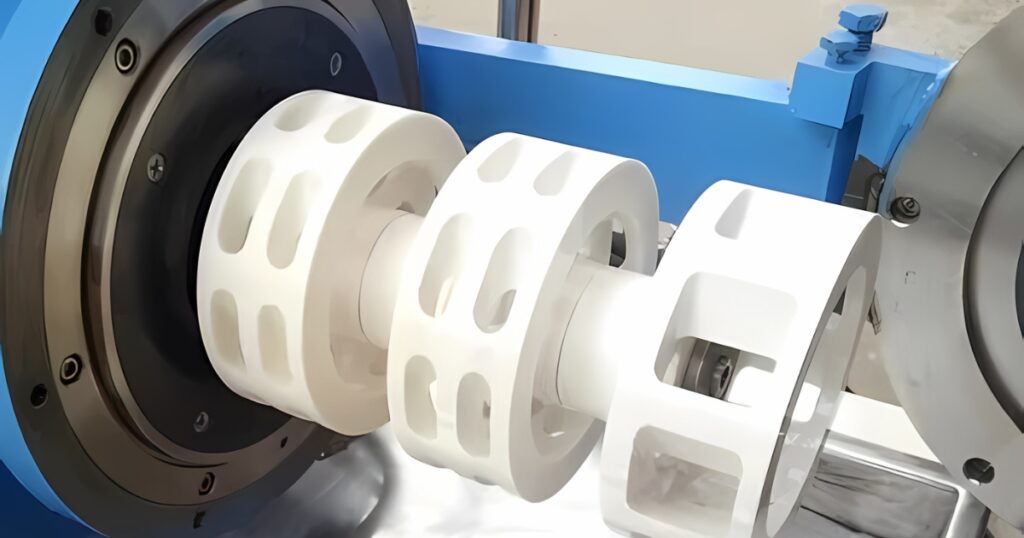
Turbo mills represent a more advanced option in horizontal sand milling technology products. They feature unique products with a rotor-stator combination that generates high shear forces. This results in extremely fine products with excellent dispersion characteristics.
The turbo design allows for processing of both low and high-viscosity products effectively. It maintains high throughput while ensuring uniform particle size distribution in products.
Turbo mills are often used in specialized applications like pharmaceuticals and advanced coatings products. Their adaptability gives them an edge in industries requiring precise formulations of products.
Comparison of Operational Advantages
Each type of horizontal sand mill has distinct operational advantages based on its design for products. Ordinary mills are straightforward and cost-effective products but limited to low-viscosity applications.
Wheel-pin mills provide enhanced control over viscosity levels and are suitable for medium-viscosity products. Toothed disc mills excel in handling thick materials and products while ensuring consistent quality.
Turbo mills stand out by accommodating a wide range of viscosities while producing exceptionally fine products. Each type’s effectiveness in products depends on specific application needs and material properties.
Adaptability to Viscosity Levels
Adaptability is key when selecting a sand mill type. Ordinary mills work best with low-viscosity liquids, making them ideal for standard paints and inks.
Wheel-pin mills bridge the gap by accommodating medium-viscosity materials such as adhesives or coatings. Their design offers flexibility without sacrificing efficiency.
Toothed disc mills tackle high-viscosity substances effectively, allowing manufacturers to process gels or pastes seamlessly. Turbo mills provide unmatched versatility across all viscosity ranges, catering to various industries’ unique requirements.
Understanding these variations helps manufacturers choose the right equipment for their specific needs. Selection impacts production efficiency and product quality directly.
Key Components
Grinding Chamber
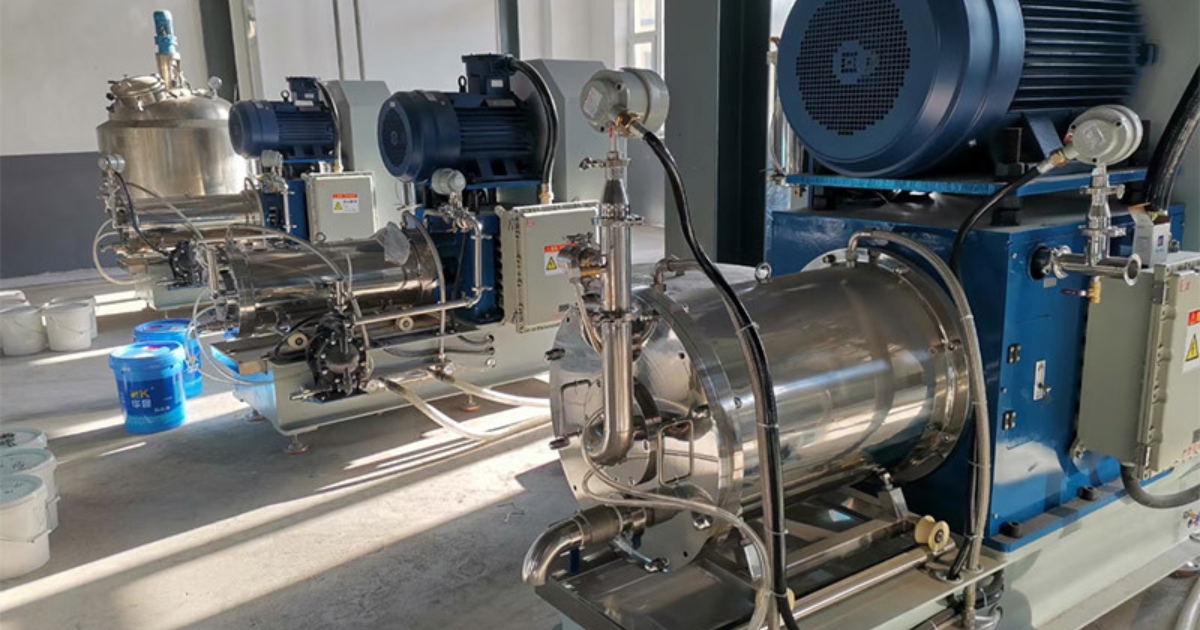
The grinding chamber serves as the core of the paint sand mill. It houses the materials during the milling process. This chamber is designed to accommodate various sizes of particles and pigments.
The structure of the grinding chamber influences the efficiency of the milling process. A well-designed chamber allows for optimal fluid flow and minimizes dead zones. This ensures that the materials are evenly processed.
Inks and other liquids enter the chamber for mixing and grinding. The design must also support high energy input, which is crucial for effective particle size reduction.
Grinding Media
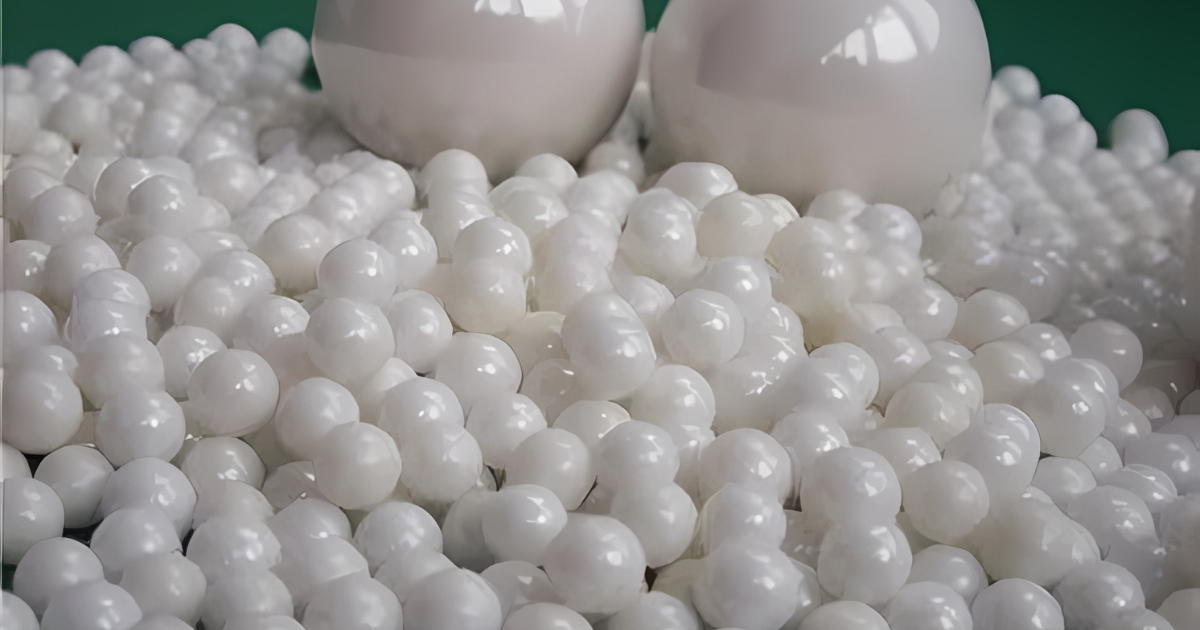
Grinding media play a critical role in the milling process. These are small beads or pins that facilitate the grinding action. They collide with the particles, breaking them down into finer sizes.
Different types of media can be used, depending on the material being processed. For example, ceramic beads are common for inks due to their durability and resistance to wear. The choice of media affects both efficiency and product quality.
The size and density of the grinding media also impact results. Smaller beads provide better dispersion but may require more energy. Selecting the right grinding media is essential for achieving desired outcomes in ink production.
Cooling System
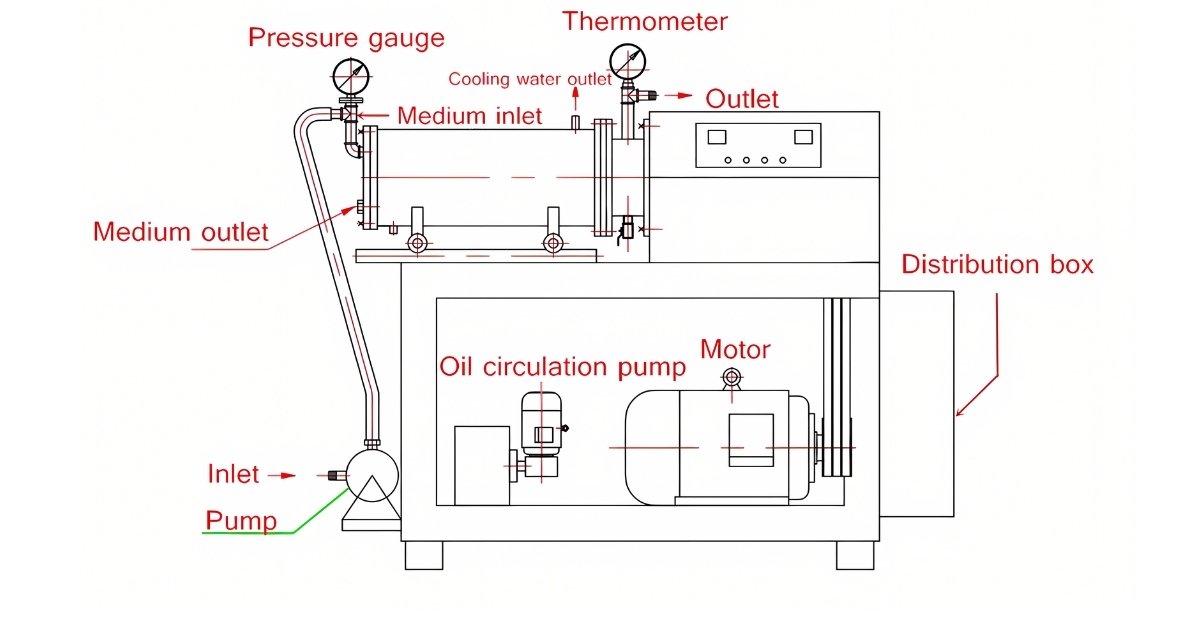
A cooling system is vital for maintaining optimal operating temperatures. High energy milling generates heat, which can affect product quality. Excessive heat can lead to changes in viscosity or even degradation of sensitive materials.
Cooling systems typically involve water or air circulation around the grinding chamber. This helps dissipate heat effectively during operation. Maintaining a stable temperature ensures consistent performance and prevents damage to materials.
Without proper cooling, equipment can overheat, leading to costly downtime. Therefore, a reliable cooling system enhances both safety and efficiency in production processes.
Control Systems
Control systems ensure consistency in product quality throughout the milling process. These systems monitor variables such as temperature, pressure, and flow rates. By maintaining these parameters within specified ranges, control systems help produce uniform results.
Modern machines often incorporate automated controls. These allow operators to adjust settings in real-time based on feedback from sensors. Such technology improves precision in ink production.
Operators benefit from having access to data analytics provided by control systems. This information can identify trends and areas for improvement in manufacturing processes.
Operating Guide
Setup Instructions
Setting up a horizontal sand mill requires careful attention to detail. Begin by placing the mill on a stable surface. Ensure that the area is clean and free from any obstructions.
Next, connect the mill to its power source. Use a suitable voltage as specified in the machine’s manual. Verify all connections are secure before proceeding.
Once connected, fill the milling chamber with the appropriate media. This could be glass beads or ceramic balls, depending on the material being processed. The correct size of media is crucial for optimal operation.
Loading Materials
Loading materials into the sand mill must be done with precision. Start with measuring the desired amount of paint or other materials. Use a scale for accuracy to ensure consistency in each batch.
Pour the measured material into the hopper slowly. Avoid overloading, as this can lead to inefficient milling and potential damage to the equipment.
Adjust the flow rate of materials entering the mill. This ensures that the milling process runs smoothly without causing blockages or excessive pressure build-up.
Monitoring Parameters
Monitoring temperature and pressure during operation is essential. High temperatures can indicate friction or inadequate lubrication. Check the temperature gauge regularly to avoid overheating.
Pressure readings should also be monitored closely. Abnormal pressure levels may signal a blockage or malfunction within the system. A sudden drop in pressure often requires immediate attention.
Keep a log of these readings throughout operation. Documentation helps in identifying trends and potential issues over time.
Safety Precautions
Safety is paramount when operating a horizontal sand mill. Always wear protective gear such as goggles and gloves. These protect against splashes and accidental contact with materials.
Ensure that all safety guards are in place before starting the machine. These guards prevent access to moving parts during operation.
Never attempt to open or service the machine while it is running. Wait until it has completely stopped before performing any maintenance tasks.
Regularly inspect equipment for wear and tear. Replace any damaged components immediately to avoid accidents.
Maintenance Tips
Regular Inspections
Operators should establish a regular inspection schedule. This helps to identify potential issues before they escalate. Key components such as pumps and motors require frequent checks. Inspecting these parts can prevent unexpected breakdowns.
Routine inspections should focus on the pump system. Look for signs of leaks or unusual noises. These could indicate problems that need immediate attention. Check the electrical connections for any signs of wear. Maintaining these components ensures reliable operation.
Regularly reviewing the bead mill’s performance is also crucial. Operators should monitor output consistency and efficiency. Any sudden changes may signal underlying problems. Addressing these issues early can save time and money.
Cleaning Procedures
Maintaining hygiene in bead mills is vital for product quality. Operators should implement strict cleaning procedures. This prevents contamination and ensures safe operation.
Cleaning should occur after each production cycle. Use appropriate cleaning agents that do not harm the equipment. Focus on areas where materials might accumulate, such as the tank and pipes.
Operators must ensure that all residues are removed thoroughly. This includes pigments or chemicals used during processing. Failure to clean properly can lead to cross-contamination in future batches.
Lubrication Importance
Lubricating moving parts is essential for smooth operation. Proper lubrication reduces friction and wear on components. Operators should use the recommended lubricants for their specific equipment.
Regular lubrication intervals should be established based on usage patterns. For example, daily operations may require more frequent lubrication checks than less frequent use.
Pay attention to bearings, gears, and other moving parts during maintenance. Signs of insufficient lubrication include unusual noises or overheating components. Addressing these issues quickly can prolong the life of the machinery.
Signs of Wear and Tear
Operators must remain vigilant for common signs of wear and tear. Identifying these signs early can prevent costly repairs or downtime.
Look out for vibrations that seem excessive during operation. Unusual vibrations often indicate misalignment or worn-out parts. Another sign is a decrease in performance efficiency over time.
Listen for strange sounds coming from the machinery. Grinding or squeaking noises may suggest that components need replacement or adjustment. Operators should document any irregularities during inspections to track patterns over time.
Applications in Various Industries
Paint Industry
Horizontal sand mills play a crucial role in the paint and coating industries. These machines ensure uniform particle size and consistent color dispersion. They achieve this through high shear forces that break down pigments effectively.
Manufacturers use these mills to produce various types of paints, including water-based and solvent-based options. The efficiency of sand mills allows for faster production cycles. This results in reduced costs and improved product quality.
The ability to control temperature during milling is vital. It prevents degradation of sensitive materials like certain pigments. This control contributes to the longevity and stability of the final product.
Pharmaceutical Sector
Sand mills find significant applications in pharmaceuticals. They are essential in drug formulation processes. These machines help create fine suspensions and emulsions, which are vital for effective drug delivery.
The milling process ensures uniformity in particle size, which is crucial for dosage accuracy. Manufacturers rely on sand mills to produce formulations that meet strict regulatory standards.
For example, when creating liquid medications, achieving a consistent texture is necessary. Sand mills facilitate this by breaking down active ingredients into smaller particles. This increases bioavailability and effectiveness of the medication.
Inks and Dyes Production
The ink and dye industry also benefits from horizontal sand mills. These machines provide high shear mixing, which is necessary for producing vibrant colors. The capability to disperse pigments evenly leads to better color quality.
Manufacturers use sand mills to create various ink types, such as printing inks and specialty inks. The equipment allows for customization based on specific client needs. This flexibility helps companies stay competitive in the market.
Sand mills contribute to the production of dyes used in textiles and other materials. Consistent particle size ensures even application during dyeing processes. This results in superior colorfastness and overall quality of the dyed products.
Cosmetics Manufacturing
Cosmetics manufacturing relies heavily on horizontal sand mills for achieving fine textures. These machines are essential in formulating creams, lotions, and makeup products. A smooth texture is critical for consumer satisfaction.
The milling process breaks down raw materials into ultrafine particles. This results in a luxurious feel when applied to the skin. Manufacturers prioritize this aspect for skincare products to enhance user experience.
Sand mills also allow for the incorporation of active ingredients without compromising their efficacy. For instance, antioxidants and vitamins can be blended seamlessly into formulations. This ensures consumers receive maximum benefits from their cosmetic products.
Technical Specifications
Capacity
These horizontal sand mills come in various capacities. Common sizes range from 5 liters to over 100 liters. Larger models can handle high viscosity materials effectively. Smaller units are ideal for laboratory settings, allowing precise control during testing.
Power requirements vary depending on the model. Most standard units operate between 5 kW to 30 kW. The power needed increases with capacity and viscosity of the material processed. Users must consider these factors when selecting equipment.
Dimensions of the mills also vary widely. A compact model may measure around 1 meter in length, while larger ones can exceed 2 meters. Space availability in the facility plays a crucial role in choosing the right size.
Particle Size
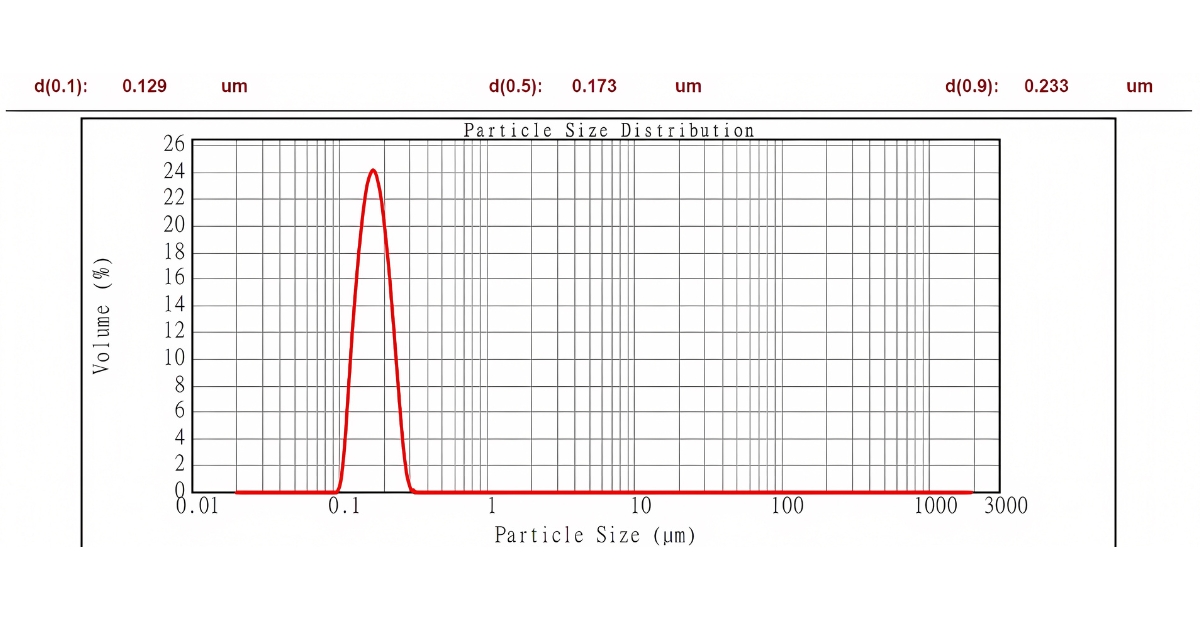
Horizontal sand mills achieve a wide range of particle sizes. Typical outputs range from 1 micron to 50 microns. This capability is essential in industries like coatings and inks, where particle size affects product quality.
The type of medium used influences particle size as well. Harder media can produce finer particles. Glass, zirconia, and steel are common options for milling media. Each offers different benefits based on material properties.
Achieving smaller particle sizes requires careful control of temperature and viscosity during milling. Maintaining optimal conditions ensures consistent results. Operators should monitor these parameters closely throughout the process.
Materials
These mills process various materials effectively. Suitable materials include paints, inks, and coatings. They also handle ceramics, pharmaceuticals, and food products.
Material hardness affects the choice of milling medium. Softer materials may require softer media to avoid contamination. For example, glass beads work well with less abrasive substances.
High-viscosity materials may need special attention. These include gels or thick pastes that resist flow. Operators should adjust turbine speeds accordingly to maintain proper flow rates.
Customization Options
Customization options enhance the versatility of horizontal sand mills. Manufacturers often offer adjustable features to meet specific needs. Key options include variable speed controls and different turbine designs.
Users can select custom tank sizes for unique production needs. Some mills allow for interchangeable milling media to accommodate various applications. This flexibility benefits companies that deal with multiple products.
e models feature integrated cooling systems. These systems maintain optimal temperatures during processing, especially for heat-sensitive materials. Such enhancements improve efficiency and product quality.
Comparing Horizontal and Vertical Mills
Design Differences
Horizontal sand mills and vertical sand mills have distinct designs. Horizontal sand mills feature a horizontal orientation of the grinding chamber. This design allows for better flow of materials. The media is kept in motion by a rotating shaft with discs.
Vertical sand mills have a vertical orientation. The grinding media sits at the bottom of the chamber. This design can lead to different operational dynamics. In vertical mills, gravity aids in moving particles downward. Each mill type has its own advantages based on these designs.
Efficiency in Grinding
Efficiency varies between horizontal and vertical sand mills. Horizontal sand mills often provide superior grinding capabilities. They can achieve finer particle sizes more quickly. This is due to their design that enhances media movement.
Vertical sand mills may be less efficient in certain applications. They can take longer to achieve similar results compared to horizontal models. However, they excel in specific scenarios, such as when dealing with high-viscosity materials. Understanding these efficiencies helps users choose the right milling machine for their needs.
Application Suitability
Applications differ significantly for each type of mill. Horizontal sand mills are ideal for coatings, inks, and paints. Their ability to produce fine dispersions makes them suitable for these industries.
Vertical sand mills find their strength in applications like cosmetics and pharmaceuticals. They handle viscous materials well, making them preferred for certain formulations. Choosing the right mill depends on the specific application requirements.
Cost Implications
Cost implications also vary between horizontal and vertical sand mills. Horizontal models generally come at a higher initial investment. They offer advanced features that justify this cost over time.
Vertical sand mills tend to have lower upfront costs. However, they may require more maintenance, which can increase long-term expenses. Users should evaluate both initial costs and ongoing maintenance when selecting a mill.
Space Requirements
Space requirements differ based on mill design as well. Horizontal sand mills usually need more floor space due to their length. Their layout requires careful planning in production environments.
Vertical sand mills occupy less floor space but may need additional height clearance. This factor can impact facility layout and design decisions. Understanding these spatial needs helps ensure proper installation and operation.
Innovations in Bead Mill Technology
Recent Advancements
Recent advancements in grinding technology focus on improving efficiency. Modern bead mills feature designs that enhance the milling process. High efficiency bead mills can achieve finer particle sizes faster than traditional bead mills. This results in reduced production times and lower operational costs.
These machines utilize advanced rotor designs. They create a more uniform distribution of beads within the mill. This uniformity leads to better grinding performance and increased throughput. The integration of turbo type bead mills also contributes to these improvements. These mills operate at higher speeds, allowing for quicker processing of materials.
Laboratory sand mills have also seen enhancements. New models offer precise control over the milling process. Operators can adjust parameters like speed and pressure easily. This flexibility allows for experimentation with different materials and formulations.
Automation and Control Systems
Automation plays a key role in modern bead mill technology. Many new bead mill machines incorporate smart control systems. These systems monitor various aspects of the milling process in real-time. They ensure optimal conditions for grinding, which increases overall efficiency.
Automated systems reduce the need for manual intervention. Operators can set specific parameters and let the machine run independently. This not only saves time but also minimizes human error during operation.
Data collection is another advantage of automated systems. Machines can log performance metrics, providing valuable insights into production processes. This information helps manufacturers make informed decisions about equipment usage and maintenance.
Energy Consumption Reduction
Innovations aim to reduce energy consumption during operation. Traditional disc type bead mills often consume large amounts of energy. Newer models are designed with energy efficiency in mind.
High energy wet grinding mills utilize advanced technologies to minimize power usage. These machines optimize the grinding process, requiring less energy to achieve desired results. Manufacturers report significant savings on energy costs with these newer machines.
The development of nanometer sand mills also contributes to this goal. These mills require less energy while producing extremely fine particles. Their design allows for effective grinding without excessive power consumption.
Environmentally Friendly Materials
Environmental concerns drive innovation in grinding media materials as well. Traditional bead mill operations often rely on materials that may harm the environment. New developments focus on creating eco-friendly alternatives.
Manufacturers now produce grinding beads from sustainable resources. These materials perform effectively without compromising quality or efficiency. Using environmentally friendly materials helps companies meet regulatory standards.
The shift towards greener practices reflects broader industry trends. Companies increasingly prioritize sustainability in their operations. By adopting these innovations, they contribute to a healthier planet while maintaining productivity.
Environmental Impact
Ecological Footprint
Sand mill operations have a noticeable ecological footprint in various industries. These mills are used in paint, coatings, and ink production. They grind materials to create fine particles. This process can lead to environmental issues if not managed properly.
High energy density is required for efficient milling. This can result in significant energy consumption. The production process often generates waste that needs careful handling. If not disposed of correctly, this waste can harm local ecosystems.
Water usage is another concern. Sand mills often require water for cooling and cleaning. Excessive water use can strain local resources. It may also lead to contamination if chemicals from the milling process enter water sources.
Waste Management Practices
Effective waste management practices are crucial in sand mill operations. Proper disposal of by-products minimizes environmental risks. Companies must implement systems to manage waste efficiently.
Recycling materials is one approach to reduce waste. Many industries recycle sand and other materials from the milling process. This reduces the need for new raw materials and lowers production costs.
Another practice involves using closed-loop systems. These systems recirculate water and other resources within the mill. This reduces discharge into the environment and conserves resources.
Regulations play a key role in shaping these practices. Compliance with environmental standards ensures companies take responsibility for their waste.
Advancements in Sustainability
Recent advancements focus on reducing emissions and improving sustainability in sand mill technology. New designs aim to increase efficiency while lowering energy consumption. These innovations help decrease the overall carbon footprint.
Developers also explore alternative materials for milling processes. Using eco-friendly substances can reduce harmful emissions during production. This shift supports a more sustainable approach to manufacturing.
Monitoring systems have improved as well. Real-time data collection allows companies to track energy use and emissions closely. This information helps identify areas for improvement.
Sustainable practices not only benefit the environment but also enhance company reputations. Consumers increasingly prefer products made with eco-friendly methods.
Role of Regulations
Regulations significantly influence environmentally responsible milling practices. Governments set standards that companies must follow to minimize their ecological impact. Compliance ensures that businesses operate within safe limits for emissions and waste disposal.
These regulations often promote research into greener technologies. Funding and incentives encourage companies to adopt sustainable practices. As a result, businesses are more likely to invest in innovative solutions.
Failure to comply with regulations can lead to penalties and fines. This motivates companies to prioritize environmental stewardship. The pressure from regulators pushes industries toward better practices.
Closing Thoughts
The exploration of horizontal bead mills reveals their critical role in various industries, particularly in paint production. Their operational efficiency, diverse applications, and innovative advancements underscore their significance. Understanding the key components and maintenance practices can enhance performance and longevity.
For those interested in optimizing their processes with horizontal bead mills, further inquiries are encouraged. They may visit z-mixer.com to fill out a contact form or reach out directly for expert guidance and support. This proactive approach can lead to improved outcomes and greater industry insights.
Frequently Asked Questions
How do horizontal bead mills work?
Horizontal bead mills operate by using a rotating shaft to agitate beads within a chamber. This agitation generates shear forces that disperse and grind materials, achieving a fine particle size.
What are the types of horizontal bead mills?
There are several types of horizontal bead mills, including disc type, pin type, and turbine type. Each variation is designed for specific applications and material properties.
What are the key components of a horizontal bead mill?
Key components include the grinding chamber, agitator shaft, grinding media (beads), and circulation system. These elements work together to facilitate efficient milling processes.
How should one maintain a horizontal bead mill?
Regular maintenance includes cleaning the grinding chamber, inspecting the agitator and seals, and monitoring bead wear. Following manufacturer guidelines ensures optimal performance and longevity.
In which industries are horizontal bead mills commonly used?
Horizontal bead mills are widely utilized in industries such as paint, ink, coatings, pharmaceuticals, and food processing. They effectively reduce particle size in various formulations.
What are the technical specifications to consider?
Technical specifications include milling capacity, motor power, bead size range, and material compatibility. These factors determine the suitability of a mill for specific applications.
What innovations exist in bead mill technology?
Recent innovations include improved energy efficiency, advanced control systems, and enhanced materials for grinding media. These advancements aim to optimize performance and reduce environmental impact.